Optimizing Diesel Generator Performance through Corrective Maintenance
Introduction
Diesel generators are an essential component of many industrial and commercial facilities, providing backup power in the event of an electrical grid failure. These generators play a crucial role in ensuring the continuous operation of critical systems, such as data centers, hospitals, and manufacturing plants. To ensure the reliable performance of a diesel generator, it is essential to implement a proactive maintenance strategy that includes both preventive and corrective maintenance activities. Corrective maintenance, in particular, focuses on addressing issues that arise unexpectedly and can help prevent costly downtime and repairs. In this article, we will explore the importance of corrective maintenance for diesel generators and provide practical tips for optimizing their performance.
Importance of Corrective Maintenance for Diesel Generators
Corrective maintenance, also known as reactive maintenance, involves addressing issues that arise unexpectedly or after a failure has occurred. While preventive maintenance aims to prevent failures through regular inspections and maintenance activities, corrective maintenance is essential for addressing unforeseen issues and ensuring the prompt restoration of generator functionality. By implementing an effective corrective maintenance strategy, facility managers can minimize downtime, reduce repair costs, and extend the lifespan of their diesel generators.
One of the primary benefits of corrective maintenance is its ability to address issues promptly and efficiently. When a diesel generator fails unexpectedly, it can disrupt operations and cause significant downtime, leading to financial losses and potential safety risks. By having a well-defined corrective maintenance plan in place, facility managers can respond quickly to generator failures and implement the necessary repairs to restore functionality. This proactive approach can help minimize the impact of failures and ensure the continuous operation of critical systems.
Corrective maintenance also plays a vital role in identifying underlying issues that may contribute to generator failures. By conducting thorough diagnostics and root cause analysis during corrective maintenance activities, maintenance technicians can pinpoint the source of the problem and implement targeted solutions to prevent future failures. This proactive approach not only helps address immediate issues but also improves the overall reliability and performance of the diesel generator over time.
In addition to minimizing downtime and addressing underlying issues, corrective maintenance can also help extend the lifespan of diesel generators. By promptly addressing failures and implementing timely repairs, facility managers can prevent minor issues from escalating into major problems that require costly repairs or replacement of components. This proactive approach can help maximize the longevity of the generator and ensure its continued reliability for years to come.
Best Practices for Implementing Corrective Maintenance for Diesel Generators
To maximize the effectiveness of corrective maintenance for diesel generators, facility managers should follow best practices and implement a structured approach to addressing unexpected failures. The following tips can help optimize the performance of diesel generators through effective corrective maintenance:
1. Establish a Comprehensive Maintenance Plan: Before implementing corrective maintenance activities, it is essential to develop a comprehensive maintenance plan that outlines the procedures and protocols for addressing unexpected failures. The plan should include details on how failures will be reported, how maintenance technicians will be notified, and the steps to be taken to address different types of issues.
2. Conduct Regular Inspections and Monitoring: In addition to reactive maintenance, it is crucial to conduct regular inspections and monitoring of the diesel generator to identify potential issues before they escalate. By monitoring key performance indicators, such as fuel consumption, oil levels, and temperature readings, maintenance technicians can detect early warning signs of potential failures and take proactive measures to address them.
3. Prioritize Critical Components: When conducting corrective maintenance activities, it is essential to prioritize the inspection and repair of critical components that are essential for the operation of the generator. By focusing on key components, such as the engine, alternator, and fuel system, maintenance technicians can ensure the reliable performance of the generator and minimize the risk of unexpected failures.
4. Implement a Root Cause Analysis Process: To prevent recurring issues and improve the overall reliability of the diesel generator, facility managers should implement a root cause analysis process during corrective maintenance activities. By identifying the underlying causes of failures and implementing corrective actions to address them, maintenance technicians can prevent similar issues from occurring in the future.
5. Document Maintenance Activities: Keeping detailed records of corrective maintenance activities is essential for tracking the performance of the diesel generator and identifying trends or patterns that may indicate potential issues. By documenting repairs, inspections, and root cause analysis findings, facility managers can gain valuable insights into the health of the generator and make informed decisions about future maintenance activities.
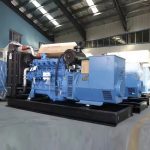
6. Invest in Training and Skills Development: To ensure the success of corrective maintenance activities, it is essential to invest in training and skills development for maintenance technicians. By providing ongoing training on diesel generator maintenance best practices, troubleshooting techniques, and safety protocols, facility managers can empower their maintenance team to effectively address unexpected failures and optimize the performance of the generator.
Conclusion
Corrective maintenance plays a critical role in optimizing the performance of diesel generators and ensuring the reliable operation of critical systems. By implementing a proactive corrective maintenance strategy that focuses on addressing unexpected failures promptly and efficiently, facility managers can minimize downtime, reduce repair costs, and extend the lifespan of their generators. By following best practices, such as establishing a comprehensive maintenance plan, conducting regular inspections, prioritizing critical components, implementing root cause analysis, documenting maintenance activities, and investing in training and skills development, facility managers can optimize the performance of their diesel generators and ensure the continuous operation of their facilities. With a proactive approach to corrective maintenance, facility managers can maximize the reliability and longevity of their diesel generators and minimize the risk of unexpected failures.